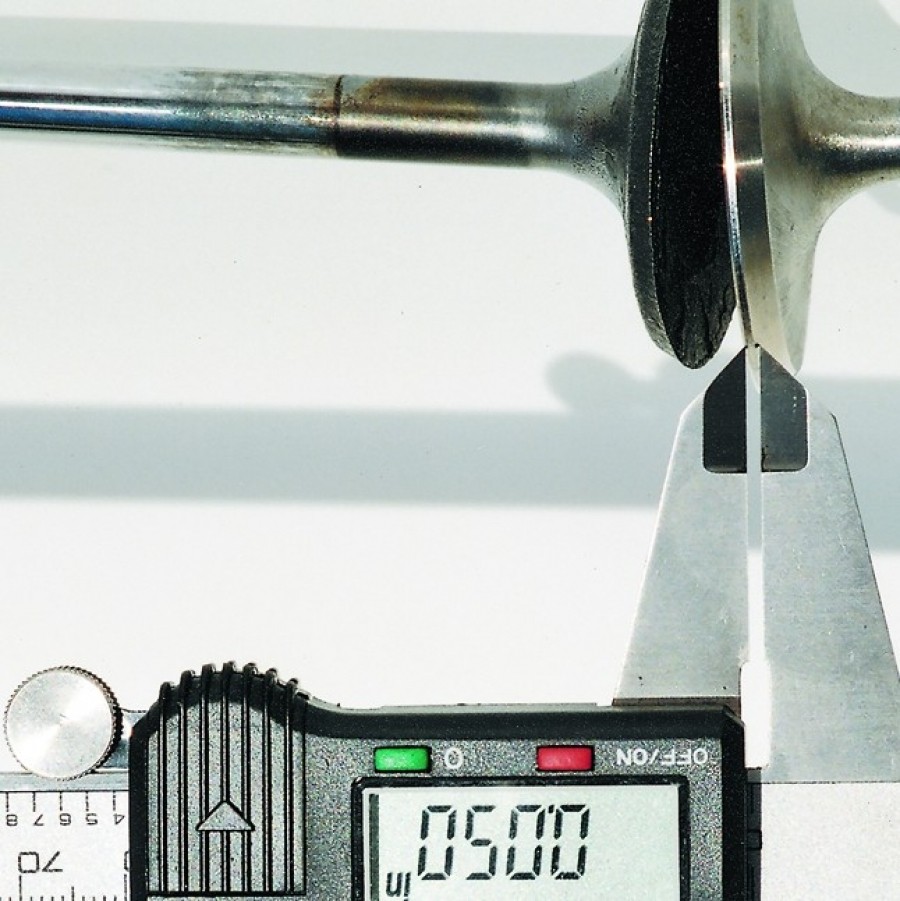
A high performance marine engine deserves high performance valves and a high performance valve job. What are high performance valves and what is a high performance valve job? Hang on while we take you there. You may not be doing the job yourself or have the equipment to do so but it is reassuring to know whether or not the job is done right.
In this article we will deal with some of the operations involved in reconditioning the heads to make them as good as or better than new. Before any final seat grinding can be done, the valve guides must be checked. If there is significant wear they should all be replaced. Excessive valve stem to bore clearance (over 0.003”) will cause excessive oil consumption and in extreme cases valve breakage. Insufficient clearance will result in noisy and sticky valves, which again can cause engine damage if they come in contact with the pistons. Valve stem clearances are 0.0010” to 0.0025”. Because the exhaust valves run hotter than the intake, particularly on supercharged engines, they need 0.0002” to 0.0005” more clearance.
It is essential that valve guide bores be free from carbon or dirt to achieve proper centering of the pilot in the valve guide, to ensure concentricity. The machine for finishing the valve seats is indexed off the valve guide in the head. Once guides are acceptable, the seats can be finish ground or cut depending on the method being used.
Another important factor that must be taken into consideration when preparing the valve seats is valve head cooling. The only time heat can disperse from the head of the valve to the cylinder head is when the valve is momentarily on its seat. Proper valve seat diameter will ensure sufficient heat transfer; too narrow a seat, although good for performance on a race engine, is not good for endurance on a marine engine.
To order a back issue call (800) 461-9128 or sign in to read entire article
The intake valve is cooled by the air/fuel mixture therefore its seat can be as narrow as 0.040” to 0.060”. The exhaust valve, on the other hand, operates in a much hotter environment – therefore the seat must be 0.060” to 0.080” and as much as 0.090” for a supercharged engine in a marine application.
Before they can be ground, each valve stem is checked for wear with a micrometer, any which are not within spec are replaced. Then they are cleaned on a wire wheel and carefully inspected for cracks and warp; again some may have to be replaced. The valves that pass inspection can then be ground. Valves that are pitted must be refaced to the proper angle. If a valve is excessively pitted it may not be possible to reface it without removing so much material that a knife edge occurs. A knife edge can lead to breakage, tuliping, burning or pre-ignition due to heat localizing on the knife edge. If the valve margin (edge) is less than 1/32in. after grinding the valve must be replaced. Exhaust valve margin in supercharged marine engines should be no less than 0.090 wide for durability reasons.
Hand lapping the valves into the seats is often considered unnecessary with the accuracy of the valve and seat reconditioning equipment most machine shops use today. Lapping is a simple do-it-yourself operation that provides a way to visibly check the accuracy of the machine work, and also results in a more perfect seal than any other method. A few dabs of fine lapping compound are applied to the area of the valve which contacts the seat. Then the suction cup of the lapping stick is stuck to the head of the valve and rotated back and forth between the palms. The valve is raised off the seat and repositioned occasionally to assure even distribution of the lapping compound. When the valve begins to turn easier the lapping compound is no longer cutting. Remove the valve from the head, wipe the compound off the valve and seat. There will be a gray ring on the seat and the valve face where it contacts the seat. If the gray ring is not consistent around the valve face, the valve was not machined correctly. If the gray ring is narrower or almost fades out in one area, try lapping the valve again – sometimes it takes two or three repetitions of the lapping process to obtain a good seat, depending on the pressure exerted.
All this attention to detail is conducive to efficiently producing more power while consuming the same or less fuel. In the next section we will explore some modifications that will increase the efficiency of the heads.